Has Your Rebuilt Cylinder Been Tested?
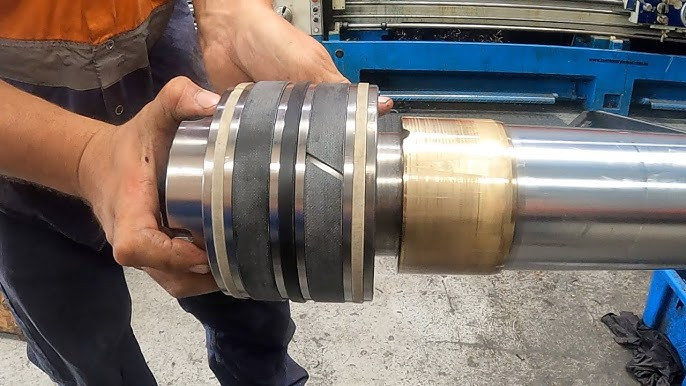
Industrial machinery relies on hydraulic cylinders for lifting heavy loads and controlling motion in various ways. Over time, cylinders may require rebuilding to restore their functionality and extend their lifespan. However, simply rebuilding a cylinder is not enough to ensure it performs. Testing is a critical step in the process to guarantee safety, efficiency, and reliability.
The Importance of Cylinder Testing
Cylinder testing is a crucial step in the rebuilding process, ensuring that the cylinder functions as intended and meets performance standards. Neglecting testing can lead to various issues, including:
Safety Concerns: Faulty cylinders can pose significant safety risks. Inadequate testing may result in unforeseen failures, putting workers and equipment at risk.
Downtime and Cost: A cylinder that fails unexpectedly can lead to costly downtime and unplanned repairs. This can have a considerable impact on production schedules and maintenance budgets.
Reduced Efficiency: Inefficient cylinders can lead to reduced productivity and energy wastage, impacting the overall efficiency of industrial operations.
Environmental Impact: Leaking or malfunctioning cylinders can release hydraulic fluids into the environment, causing pollution and potential damage to sensitive ecosystems.
Testing Methods
Several testing methods are employed to ensure that a rebuilt cylinder is in proper working condition. Some of the most common methods include:
Pressure Testing: Pressure testing involves subjecting the cylinder to high-pressure conditions to check for leaks and evaluate its ability to withstand the intended operating pressure.
Functionality Testing: This testing ensures that the cylinder operates as intended, including extending and retracting smoothly and accurately. It also evaluates the cylinder's ability to perform its specific functions.
Leakage Testing: Leakage testing involves monitoring the cylinder for any fluid leaks, which can result from damaged seals or internal components.
Load Testing: Load testing assesses the cylinder's ability to lift or support a specific load, ensuring that it can perform the required tasks safely and efficiently.
Endurance Testing: Endurance testing simulates continuous operation under extreme conditions to assess the cylinder's durability and longevity.
Sealing Performance Testing: This involves evaluating the sealing components, such as O-rings and gaskets, to ensure they effectively prevent fluid leakage.
Corrosion and Wear Testing: Inspection for corrosion and wear helps determine if the cylinder's components need replacement or repair.
How Flotek can help
Cylinder testing is what we do - it’s our day job. Our purpose built plant in Melbourne carries out hundreds of cylinder rebuilds each week; and every one is tested prior to being re-installed. This is a non-negotiable.
This needs to be carried out by certified professionals who are well-versed in hydraulic and pneumatic systems. Flotek has the knowledge and tools necessary to perform accurate and reliable tests, ensuring that the cylinder is in optimal working condition. Proper documentation is also a crucial part of the cylinder testing process. All test results, including pressure readings, functionality assessments, and any necessary repairs, should be recorded.
Rebuilding a cylinder can extend its lifespan and save you money by not having to get a new one. But only if they’ve been tested. Over the years Flotek has been called in to address recently rebuilt cylinders, that just haven’t been tested before recommissioning.
Testing ensures that the cylinder operates safely, efficiently, and reliably, reducing the risk of accidents and downtime, and inefficiency. Your safety, and bottom line depend on it.