The Art of Hydraulic Fault Finding
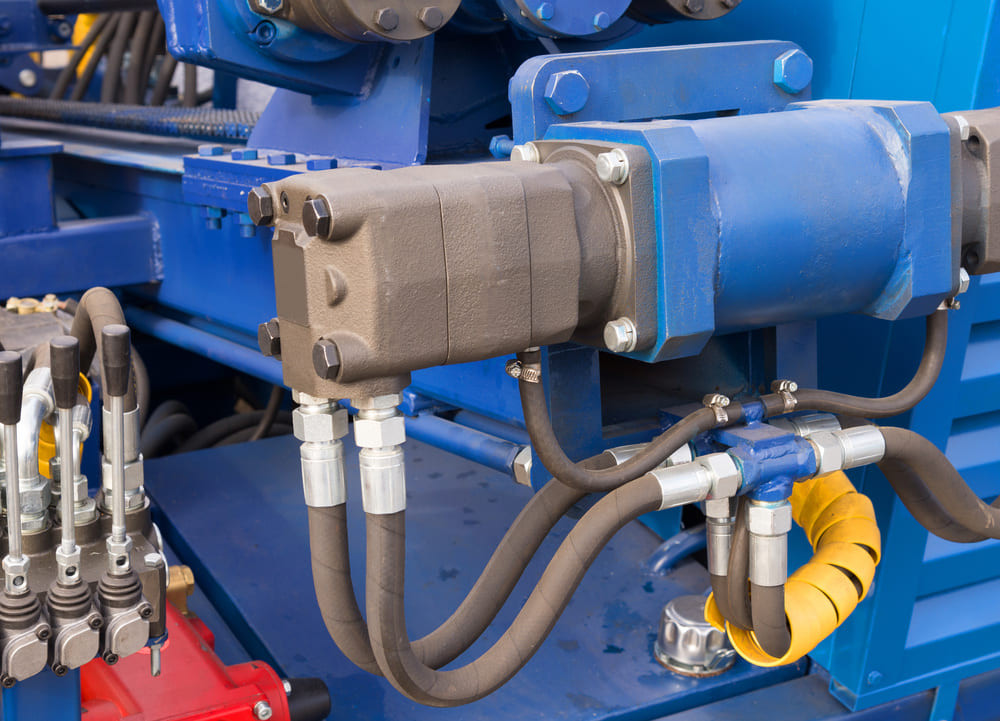
Hydraulic systems are fundamental to all moving machinery. They work by transmitting power through a fluid, typically oil, under high pressure. So when these systems fail, everything tends to grind to a halt. Mastering the art of hydraulic fault finding is a nine-step process that requires diagnostic skills, a systematic approach, and technical knowledge.
Understanding the Basics of Hydraulics
To effectively troubleshoot hydraulic systems, it’s essential to first understand how they work. A typical hydraulic system consists of FIVE core components:
Hydraulic Pump: Converts mechanical power into hydraulic energy.
Valves: Direct and control the flow and pressure of the hydraulic fluid.
Actuators (Cylinders or Motors): Convert hydraulic energy back into mechanical motion.
Reservoir: Stores hydraulic fluid.
Hydraulic Fluid: The medium through which power is transmitted.
In a well-functioning system, fluid flows smoothly, components operate efficiently, and the system delivers consistent performance. Faults arise when there are leaks, blockages, or component failures, which lead to erratic operation and movement, noise, overheating, or ultimately system failure.
The Systematic Approach to Fault Finding
Fault finding in hydraulics requires a methodical and logical process. Here’s a step-by-step guide to help diagnose problems effectively:
1. Understand the Symptoms
Before diving into the system, gather as much information as possible about the fault. Ask questions such as:
What exactly is the system failing to do?
Is there abnormal noise, vibration, or excessive heat?
When did the issue start, and has it been intermittent or constant?
These details provide important clues about the nature of the problem and help narrow down potential causes.
2. Visual Inspection
A thorough visual inspection is the first hands-on step. Look for obvious signs of trouble, such as:
Leaks: Hydraulic systems are prone to oil leaks due to high pressure. Check for visible oil around seals, hoses, and connections.
Damaged Components: Inspect hoses, fittings, and cylinders for wear, cracks, or other signs of physical damage.
Contamination: Dirt, water, or other contaminants in the system can cause malfunction. Check for signs of dirty or cloudy oil in the reservoir.
3. Check Fluid Levels and Condition
The hydraulic fluid is the lifeblood of the system. Low fluid levels can lead to cavitation (formation of air bubbles), which will damage the pump. Check the reservoir for adequate fluid levels. Additionally, inspect the condition of the fluid.
Cloudy or milky fluid could indicate water contamination.
Dark or burnt-smelling fluid might suggest overheating or degradation.
If contamination is present, the system may need to be drained and flushed before further troubleshooting.
4. Analyse Pressure Readings
Hydraulic systems rely on proper pressure to function. Using a pressure gauge, check the system pressure at various points. Common pressure-related faults include:
Low Pressure: Could be due to a failing pump, internal leaks, or pressure relief valve issues.
High Pressure: May be caused by a blocked line or a malfunctioning pressure relief valve.
Pressure Fluctuations: Can signal air in the system, incorrect settings, or faulty components.
By systematically checking pressure readings, you can identify areas where the system is not operating as it should.
5. Test Components Individually
If a visual inspection and pressure checks don’t reveal the issue, it’s time to test individual components:
Hydraulic Pump: Listen for abnormal noise, such as whining or knocking, which could indicate cavitation or wear. Test its output pressure to ensure it meets the system’s requirements.
Valves: Manually or electronically operate valves to see if they are stuck, slow, or erratic. Blockages, contamination, or wear in valve components can lead to malfunction.
Actuators (Cylinders or Motors): Check for smooth and consistent operation. Jerky or slow movement could indicate internal leaks or contamination.
By isolating and testing each component, you can pinpoint the root cause of the fault.
6. Inspect Filters and Seals
Filters and seals play a critical role in maintaining hydraulic system integrity. Blocked filters will restrict fluid flow (very bad news), leading to pressure drops and overheating. Inspect all filters and replace them if necessary. Similarly, worn seals can cause leaks, pressure loss, and contamination. Replacing damaged seals is a common maintenance task in hydraulic systems. And will rectify a lot of hydraulic system problems.
7. Monitor Temperature
Hydraulic systems are sensitive to temperature fluctuations. Excessive heat can damage components and degrade fluid. We use a thermal imaging camera or temperature sensor to check for hotspots in the system, particularly around the pump, reservoir, and actuators. Overheating is often caused by:
Overloaded systems.
Insufficient cooling (e.g., blocked coolers or fans).
Fluid contamination.
8. Air Entrapment and Cavitation
Air in the hydraulic system can lead to cavitation, where air bubbles form and collapse, causing damage to pumps and valves. Signs of air entrapment include:
Foaming in the reservoir.
Erratic actuator movement.
Noise from the pump.
To resolve this, bleed the system to remove air and check for potential sources of air entry, such as loose fittings or damaged seals.
9. Check the Control System
Many modern hydraulic systems are electronically controlled. Faults in sensors, control modules, or wiring can mimic hydraulic issues. Use diagnostic tools to check for electronic faults, such as incorrect sensor readings or communication errors. Ensure all electrical connections are secure and components are functioning as intended.
Common Hydraulic Faults and Their Causes
Slow Operation:
Cause: Low fluid levels, pump wear, or blocked filters.
Erratic Movements:
Cause: Air in the system, faulty valves, or contaminated fluid.
Overheating:
Cause: Insufficient fluid, blocked coolers, or overloading.
Pressure Drops:
Cause: Internal leaks, worn seals, or damaged hoses.
Noisy Operation:
Cause: Cavitation, air entrapment, or pump wear.
Final Thoughts: Prevention is Key
While fault-finding is an essential skill, preventing them in the first place is the key. Maybe we should have said that at the start... Regular maintenance, such as changing filters, checking fluid levels, and inspecting components, will save you $1000s in the long run. Proper system design also plays a crucial role in system reliability.
By following a systematic approach and understanding the nuances of hydraulic systems, fault finding becomes less of an art and more of a science. Combining knowledge, experience, and methodical troubleshooting techniques (as above) will do it. But if you’re not able to, Flotek is your answer. We’re the hydraulic system experts—it’s our day job!