What Causes Aeration in Your Hydraulic System?
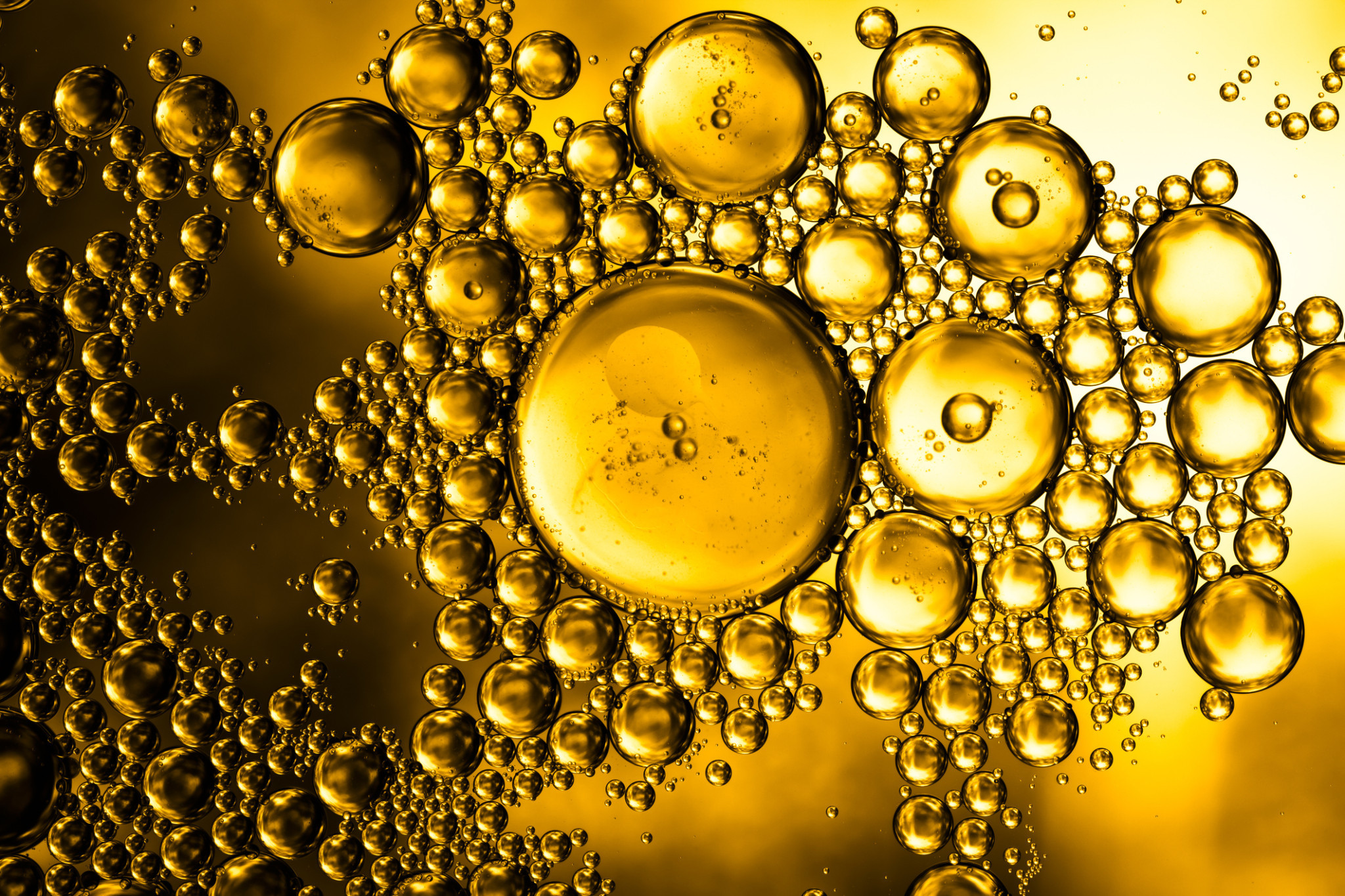
Essentially it’s air in your hydraulic system. It can be in the form of large bubbles, dissolved air, or simply foam, and can pose significant challenges for your hydraulic systems. Pump cavitation, heightened noise levels, and increased wear on hydraulic components are just a few. Understanding the various pathways through which air infiltrates hydraulic systems is crucial for maintaining operational efficiency.
What Causes of Hydraulic Fluid Aeration:
1. Leaking Inlet Lines:
Leaky pipes are a primary culprit for introducing air into hydraulic systems. Flexibility in pipes can lead to loosening if not adequately maintained, while poor-quality or incorrectly installed pipes exacerbate the issue. Threaded fittings, if not sealed properly, can also allow air in. Additionally, damaged or scored inlet flanges can further compromise sealing integrity.
2. Deteriorated System O-Rings:
Degraded o-rings lose elasticity, becoming brittle, and are prone to cracking. As a result, they lose their airtight properties, permitting air in. High operating temperatures accelerate o-ring degradation, with fluid composition, particularly those with high sulphur content, exacerbating the issue. Regular inspection and replacement of o-rings, along with temperature control measures, are essential for mitigating this source of aeration.
3. Turbulence or Sloshing in the Reservoir:
Turbulence or sloshing of fluid in the reservoir, often caused by vehicle movement on uneven terrain, induces aeration. Proper reservoir design, ensuring adequate depth and correct placement of return lines below the fluid level, mitigates turbulence-related aeration.
4. Vortexing Fluid in the Reservoir:
Poorly designed reservoir inlets can induce a vortex effect, akin to a whirlpool, promoting fluid aeration. Proper inlet design, protruding away from reservoir walls, helps counteract this phenomenon.
5. Leaking Cylinder Rod Seals:
Fast-moving cylinders can undergo extreme pressure differentials, leading to cavitation and the potential suction of air under rod seals. Anti-cavitation check valves in certain cylinders can help prevent this phenomenon.
6. Pump Shaft Seal Leakage:
Inadequacies in pump shaft seals present another avenue for air entry. Since pumps operate under a vacuum effect, compromised shaft seals facilitate direct air ingress into pump components. Excessive inlet vacuums or misalignment of shaft seals further contribute to air getting in.
7. Release of Suspended Air within the Fluid:
During startup or pressure drops, suspended air within cold hydraulic fluid is released, exacerbating aeration. Locating relief valves below the fluid level and employing baffles within the reservoir aid in getting rid of this air.
Combating Hydraulic Fluid Aeration
Hydraulic fluid aeration undermines system performance and longevity. Vigilance in identifying potential air ingress, and prompt attention to symptoms like increased noise and erratic movement are essential.